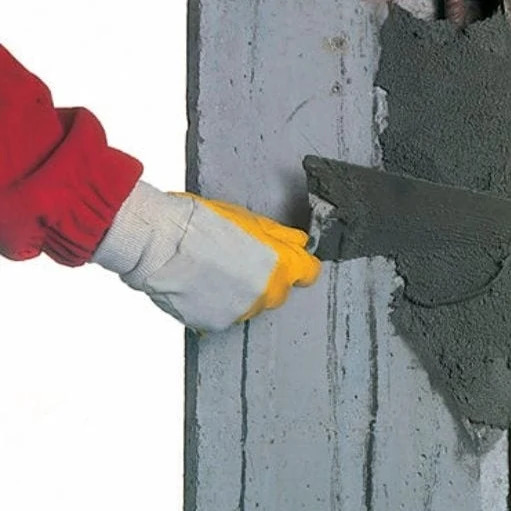
Al Hadaf Concrete Repair Services
WHY CHOOSE US?
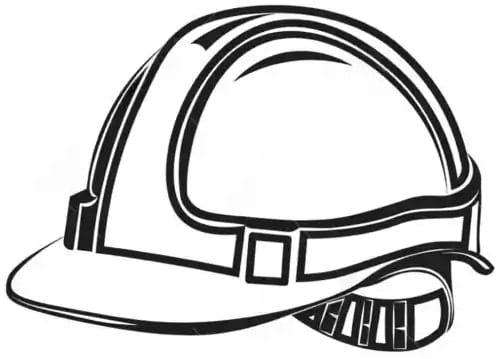
Cost-Effective Rate
Our services come at a cost-effective rate, ensuring you receive quality without breaking the bank.
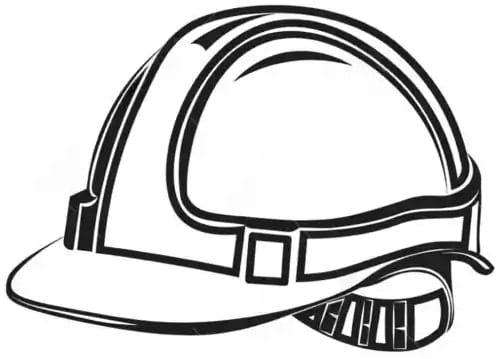
Extended Warranty
Enjoy peace of mind with our extended warranty that covers your investment for two years.
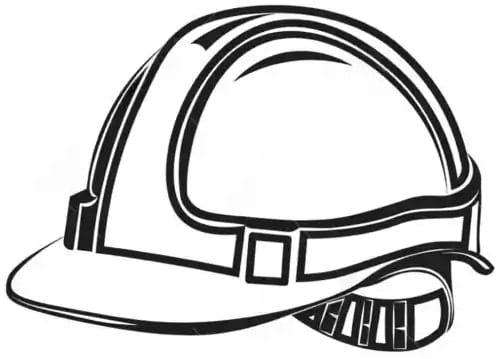
High-Grade Materials
We use only high-grade materials to guarantee durability and longevity in every project.
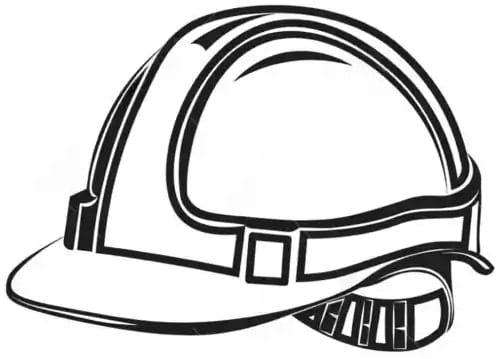
Free Annual Assessment
Take advantage of our free annual assessment to keep your concrete structures in optimal condition.
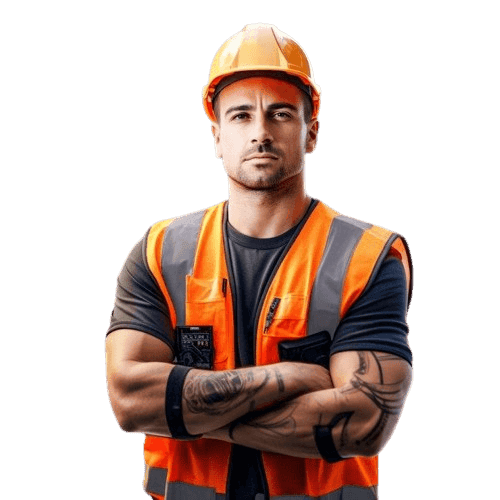
OUR CONCRETE REPAIR SERVICES
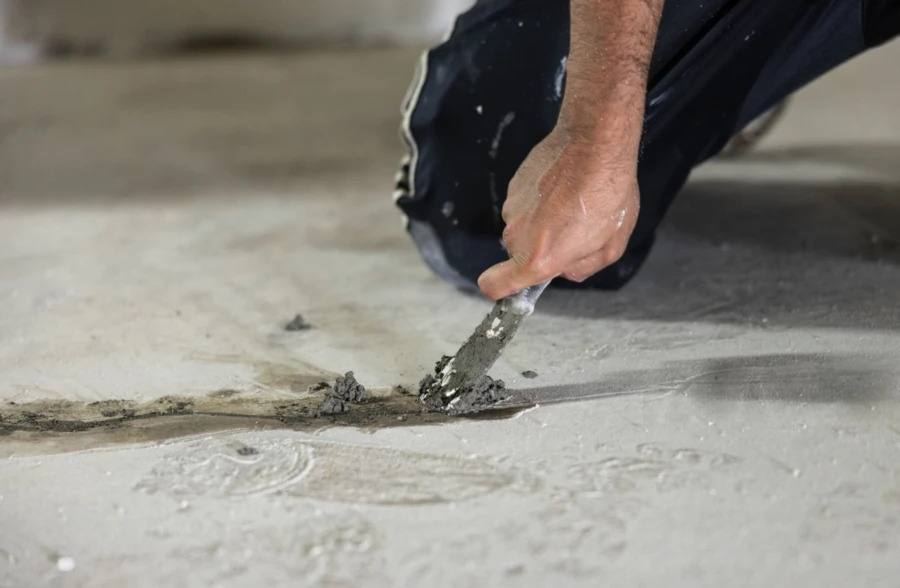
Concrete Patch Repair
Concrete patch repair is a process used to restore damaged or deteriorated concrete surfaces by applying specialized repair materials to the affected areas. It is employed to address various forms of concrete damage, such as cracks, spalling, surface erosion, and minor structural defects. Concrete patch repair aims to restore both the functionality and appearance of the concrete, preventing further deterioration and extending the lifespan of the structure
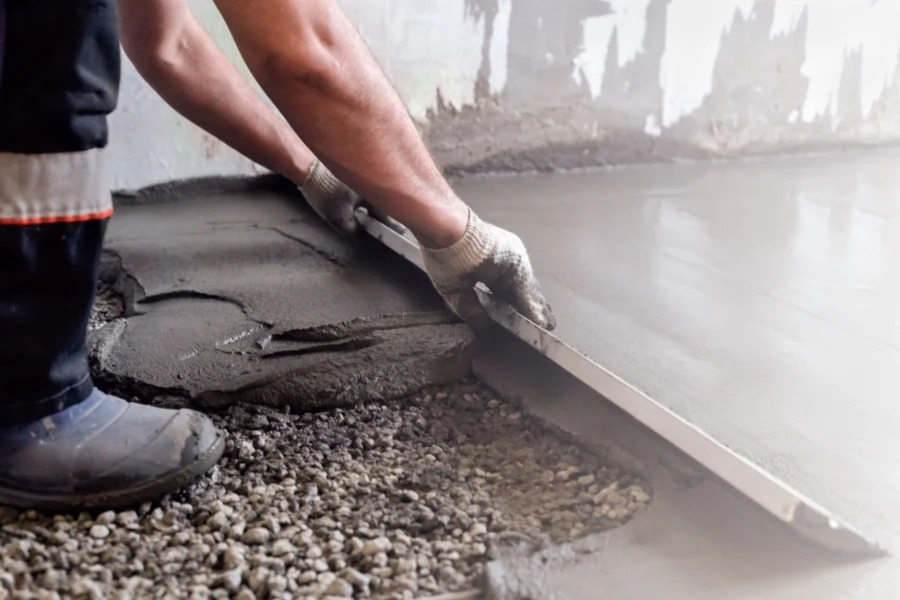
Concrete Surface Repair
Our Concrete Surface Repair Services are tailored to address the various types of damage and deterioration that concrete surfaces can experience over time. From small cosmetic blemishes to more significant structural issues, As the best concrete repair company in Dubai, Al Hadaf offers a wide range of solutions that restore the appearance, functionality, and longevity of concrete surfaces. Our expert team ensures high-quality, long-lasting repairs that stand up to Dubai’s demanding climate conditions.
Key Services:
Spall Repair: Our experts repair spalled or chipped concrete surfaces, restoring the structural integrity and preventing further deterioration.
Crack Repair: Addressing cracks in concrete surfaces using specialized techniques to prevent water penetration and restore a smooth appearance.
Patching and Resurfacing: Applying repair mortars and resurfacing materials to damaged areas, ensuring a uniform and aesthetically pleasing surface.
Joint Repair and Sealing: Repairing or replacing expansion joints, control joints, and construction joints to prevent water infiltration and maintain durability.
Surface Grinding and Polishing: Enhancing the appearance of worn or uneven concrete surfaces through grinding, polishing, and applying protective coatings.
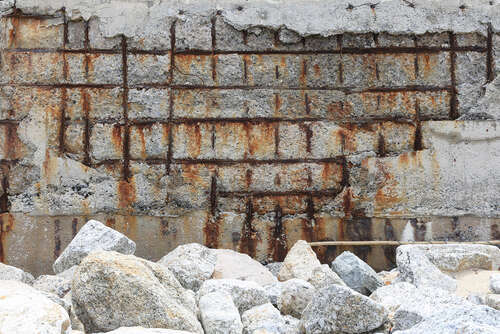
Reinforcement Corrosion Control
Corrosion of reinforcement occurs due to the presence of moisture, oxygen, and chloride ions in the concrete environment. Carbonation, exposure to deicing salts, and marine environments are common contributors to corrosion.
Cathodic protection is an electrochemical technique used to prevent corrosion in metal structures, particularly in environments where corrosion is a significant concern. This method involves introducing a sacrificial or impressed current to shift the electrochemical reactions occurring on the metal surface, effectively protecting it from corrosion.
How Cathodic Protection Works: Cathodic protection creates an electrical circuit where the metal to be protected becomes a cathode and another metal, often referred to as a sacrificial anode or impressed current anode, becomes the anode. By doing so, the protected metal is intentionally made the site of reduction reactions (cathodic reactions), preventing its corrosion.
Types of Cathodic Protection:
Galvanic (Sacrificial) Cathodic Protection:
- This method involves attaching a more reactive metal, such as zinc or aluminum, to the structure to be protected. The sacrificial anode corrodes instead of the protected metal.
- Commonly used in marine environments for structures like ship hulls, offshore platforms, and pipelines.
- Sacrificial anodes work on the principle of galvanic corrosion, where a more reactive metal corrodes sacrificially to protect a less reactive metal. The sacrificial anode is connected to the structure to be protected, forming a galvanic cell. As the anode corrodes, it releases electrons that flow through the electrolyte (usually moisture) to the structure, preventing the corrosion of the structure itself.
Types of Sacrificial Anodes:
Zinc Anodes: Commonly used in marine environments and freshwater applications. They protect steel structures, ship hulls, pipelines, and offshore platforms.
Aluminum Anodes: Used in both saltwater and freshwater environments. They are effective in protecting structures like boat hulls, bridges, and water tanks.
Magnesium Anodes: Used primarily in freshwater applications. They are employed in tanks, pipelines, and buried structures.
Impressed Current Cathodic Protection:
- An external power source is used to apply a direct current to the structure, counteracting the corrosion process.
- Often used in larger structures like bridges, storage tanks, and pipelines.
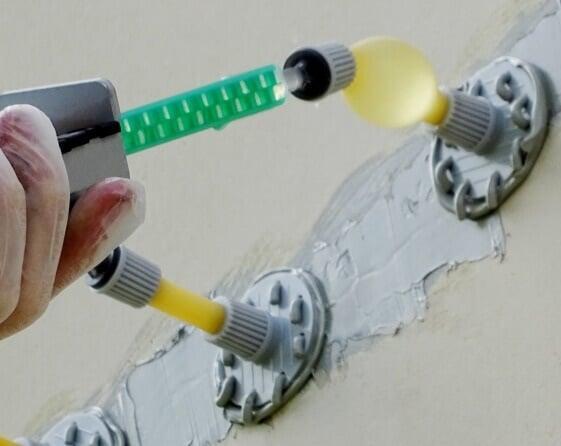
Crack Injection System
A crack injection system is a specialized technique used for repairing cracks in concrete structures. This method involves injecting specially formulated resins or grouts into the cracks, effectively sealing them and restoring the structural integrity of the concrete. Crack injection concrete repair service is a minimally invasive and cost-effective solution for preventing water infiltration, reinforcing the concrete, and preventing further damage.
Types of Crack Injection Systems:
Epoxy Injection: Epoxy resin is injected into cracks to bond and seal them. Epoxy injection is suitable for structural cracks and can restore the load-bearing capacity of the concrete.
Polyurethane Injection: Polyurethane resin is injected into cracks, expanding upon contact with moisture and creating a flexible seal. This method is effective for stopping water infiltration and non-structural cracks.
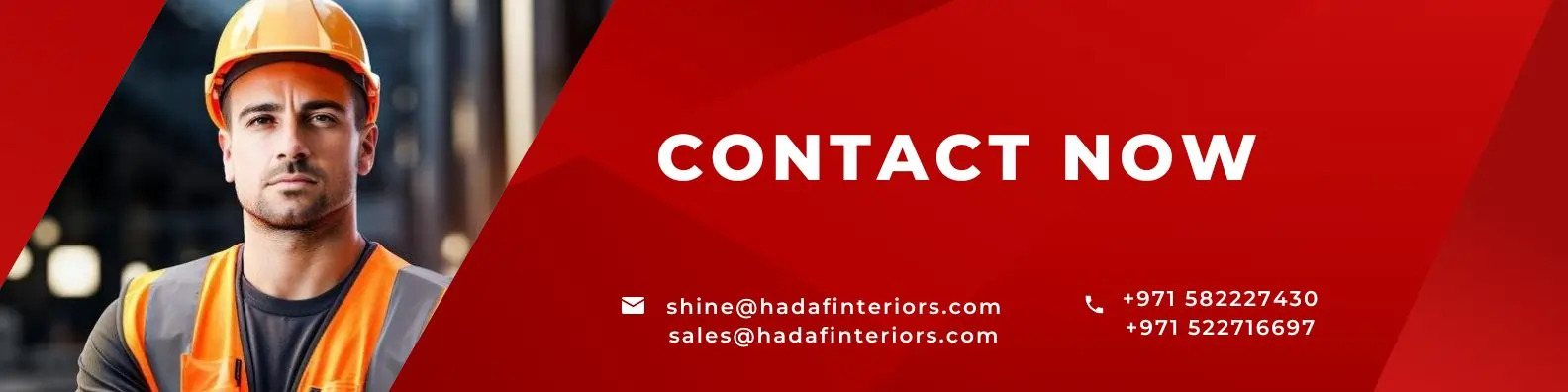
Frequently Asked Questions
Why Do You Need Concrete Repair Company in Dubai?
- Safety: Repairing cracks, spalling, and other damage prevents accidents and injuries caused by tripping hazards or structural instability.
- Structural Integrity: Addressing concrete damage promptly prevents further deterioration, preserving the strength and stability of the structure.
- Aesthetics: Repairing concrete restores its appearance, enhancing the overall look of the property and maintaining its value.
- Cost Savings: Timely repairs prevent minor issues from escalating into major problems, saving money on extensive repairs or replacements in the future.
- Longevity: Properly repaired concrete lasts longer, reducing the need for frequent maintenance and prolonging the lifespan of the structure.
Types of Concrete Repair Materials
- Portland Cement Mortar with an Admixture: A mixture that enhances the strength and durability of repairs, ensuring long-lasting concrete surfaces.
- Portland Cement Concrete with an Admixture: Ideal for larger repairs, offering improved performance and resistance against environmental damage.
- Micro-Silica Modified Portland Cement Concrete: Micro-silica adds strength and durability, particularly in areas requiring high resistance to wear and tear.
- Latex Modified Portland Cement: This material offers superior bonding and flexibility, making it ideal for high-traffic or movement-prone areas.
- Polymer Modified Portland Cement Mortar & Concrete with Non-Sag Filler: Enhanced with polymers for better bonding and crack resistance, this material ensures the repair stays intact without sagging.
- Steel Plates or Steel Section: Steel reinforcement adds structural support to weakened concrete areas, extending the lifespan of the structure.
- Fiberglass Reinforced Plastics (FRP): A lightweight but strong material used to add reinforcement without adding excessive weight to the structure.
- Carbon Strips (CFRP Laminates): Carbon fiber strips are used for structural strengthening, especially in cases where the weight of steel reinforcement would be excessive.
- Epoxy Mortar: A fast-setting and high-strength repair material suitable for patching damaged concrete surfaces.
- Shotcrete: Applied through a high-pressure hose, shotcrete is ideal for vertical and overhead repairs, providing strong adhesion to the concrete.
- Epoxy Low Viscosity Injection Resin: This material is injected into cracks to bond the fractured concrete and restore its structural integrity.
Our Concrete Repair Service Inclusions
- Survey & Repair: Our experts conduct a thorough survey of the site to identify cracks and structural weaknesses. This helps us determine the most effective repair techniques, ensuring longevity and durability.
- Surface Preparation: Proper surface preparation is crucial for achieving strong adhesion between the new material and the existing concrete. We use various techniques like chemical cleaning and acid etching to ensure the surface is ready for repair.
- Protective Mortars and Coatings: We apply protective mortars to bond building materials, and protective coatings to reduce corrosion and extend the life of concrete surfaces.
- Corrosion Inhibitors: These are often added to repair mortars as admixtures, enhancing the strength and durability of the concrete by preventing corrosion.
- Cathodic Protection: Cathodic protection is a proven technique to prevent corrosion of steel reinforcement in concrete structures, extending their service life.
- Joint & Crack Sealing: Using flexible sealants and specialized caulking materials, we effectively seal joints and cracks to prevent water infiltration and protect the concrete from further damage.
- Structural Strengthening: We enhance the load-carrying capacity of beams, walls, and other structural elements to improve their performance and longevity, ensuring the repaired structure can handle increased loads.